Innovation Released: Innovations About Aluminum Casting
Innovation Released: Innovations About Aluminum Casting
Blog Article
Unlocking the Prospective of Light Weight Aluminum Casting: Proven Methods for Success
Light weight aluminum spreading has actually long been recognized for its adaptability and widespread applications throughout numerous markets - about aluminum casting. Discovering the complete potential of this procedure calls for even more than simply basic understanding. By carrying out tested strategies sharpened with years of market experience and advancement, makers can raise their light weight aluminum casting operations to brand-new heights of efficiency and quality. From optimizing design considerations to improving production processes, the vital depend on utilizing these strategies effectively. Join us as we explore the important aspects that can move aluminum casting in the direction of unrivaled success in today's competitive market landscape.
Advantages of Aluminum Spreading
Light weight aluminum spreading provides a plethora of benefits that make it a recommended option in various industrial applications. Among the key benefits of aluminum spreading is its lightweight nature, which contributes to fuel efficiency in markets such as vehicle and aerospace. Furthermore, light weight aluminum is very flexible, enabling for complex and intricate shapes to be conveniently created via spreading processes. This convenience in layout is a considerable benefit for markets that call for components with particular geometries.
Additionally, light weight aluminum spreading provides exceptional corrosion resistance, making it suitable for applications where direct exposure to harsh atmospheres is a worry. The material likewise displays great thermal conductivity, which is useful for sectors requiring warm dissipation, such as electronics (about aluminum casting). Aluminum is totally recyclable, straightening with the growing focus on sustainable techniques in modern production.
Style Factors To Consider for Casting
The style phase plays a crucial duty in the total success of a light weight aluminum casting project. One key consideration is the choice of suitable geometries and functions that facilitate the spreading procedure.
Moreover, factors to consider associated with parting lines, gating systems, and risers are necessary to protect against problems like porosity and contraction. It is vital to maximize the design for effective material use and lessen post-processing demands. Simulations and prototyping can be useful devices in examining and improving the spreading design before full-blown production.
Partnership between layout engineers, factories, and producers is vital to attend to any kind of possible challenges early in the layout phase. By including these considerations right into the casting layout procedure, suppliers can improve product quality, decrease expenses, and ultimately unlock the full capacity of aluminum casting.
Enhancing Casting Performance
Creating with an emphasis on enhancing material circulation and decreasing issues is vital when intending to improve casting effectiveness in light weight aluminum casting projects. To achieve this, utilizing simulation software can help in identifying potential concerns prior to the spreading procedure starts. By simulating the circulation of molten light weight aluminum, designers can readjust gating and riser designs to ensure proper filling and solidification, inevitably minimizing the view it now incident of problems such as porosity or shrinkage.
Additionally, executing proper warm therapy procedures can improve the overall casting efficiency. Warm treatment can assist enhance the mechanical residential properties of the aluminum spreading, ensuring that the last part satisfies the needed requirements. In addition, using automation and robotics in the casting process can streamline manufacturing, minimize hand-operated labor, and increase general efficiency.
Furthermore, continual monitoring and quality assurance throughout the casting process are vital for determining any type of inconsistencies and making sure that the final products meet the preferred requirements. By implementing these approaches, manufacturers can improve casting efficiency, enhance product top quality, and ultimately accomplish greater success in light weight aluminum spreading tasks.
Quality Assurance in Aluminum Spreading
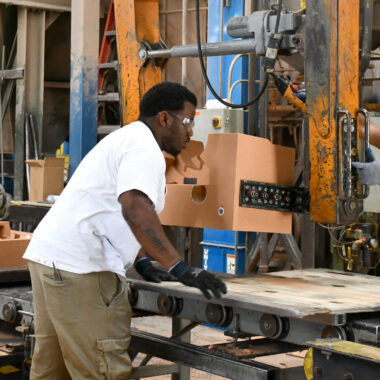
Effective quality assurance methods play a crucial function in ensuring the precision and dependability of aluminum casting procedures. Quality assurance actions in light weight aluminum spreading encompass an array of tasks targeted at promoting details standards and recognizing discrepancies that can jeopardize the end product. These techniques begin with the cautious option and assessment of basic materials to ensure their high quality and viability for the spreading procedure. Tracking and controlling the specifications of the casting process itself, such as temperature, stress, and air conditioning rates, are important action in keeping uniformity and honesty in the last products.
In addition to procedure control, quality assurance in light weight aluminum spreading involves rigorous screening and examination procedures at numerous stages of production. Non-destructive testing approaches like ultrasonic screening and X-ray assessment assistance find internal issues without compromising the honesty of the cast parts. Aesthetic assessments, dimensional measurements, and mechanical screening even more make certain that the cast components satisfy the called for specs and efficiency criteria. By applying durable quality assurance practices, light weight aluminum spreading facilities can provide items that fulfill customer expectations for integrity, efficiency, and high quality.
Making Best Use Of Success
To accomplish ideal monetary efficiency, a comprehensive method for taking full advantage of productivity within light weight aluminum casting operations should be meticulously developed and implemented. One crucial facet of making best use of success in aluminum spreading is optimizing manufacturing efficiency.
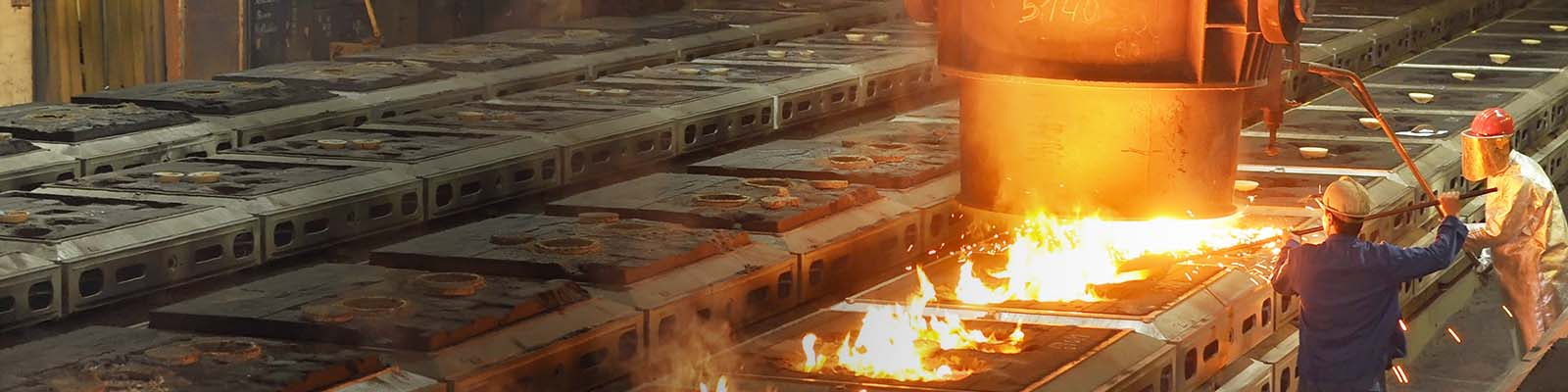
Moreover, diversifying item offerings and exploring new markets can help expand profits streams. Understanding consumer needs and market patterns can direct calculated choices to utilize on emerging opportunities. Investing in research and advancement to introduce processes or products can also drive success with differentiation and consumer complete satisfaction.
Conclusion
Finally, aluminum casting offers many benefits in terms of design sturdiness, flexibility, and cost-effectiveness. By meticulously thinking about design factors to consider, boosting casting efficiency, executing quality assurance actions, and taking full advantage of success, makers can open the complete potential of aluminum spreading. This reputable and functional procedure has proven to be a successful selection for useful site a large variety of commercial applications.
In addition, light weight aluminum is highly flexible, enabling for intricate and elaborate shapes to be quickly generated through spreading procedures.Efficient quality control techniques play a critical role in ensuring the accuracy and dependability of aluminum casting processes.In addition to process control, high quality control in light weight aluminum casting involves extensive screening and inspection procedures at various stages of manufacturing. By implementing durable top quality control methods, light weight aluminum spreading facilities can provide products that satisfy client assumptions for efficiency, quality, and integrity.
By carefully considering layout factors to consider, boosting casting performance, applying top quality control steps, and optimizing productivity, producers can open the complete capacity of aluminum casting.
Report this page